Методы испытания стали
Испытания стали проводят различными способами: от механических до динамических методов. Они включают в себя проверку на растяжение, сжатие, изгиб, излом и другие. Процедура позволяет поиск скрытых дефектов на металлических заготовках. Для строительных компаний и подрядчиков особенно важно знать показатели стали на растяжение. Данная проверка позволит уберечь конструкцию от нештатных ситуаций (деформации, трещины, аварии, обрушения).
Нержавеющая сталь и стальной прокат – изделия, которые широко используют архитекторы и строительные компании для создания артобъектов, возведения строений, обустройства жилых и нежилых помещений. Определение физико-химических характеристик готовой продукции касается ее назначения и эксплуатационных нагрузок. Методы испытания стали позволяют оценить свойства сплава и качества сырья.
Динамические методы испытания стали
Проведение исследований осуществляется в соответствии с обновленным ГОСТ 9454-78. В качестве образцов используют изделия с квадратным сечением со сторонами 10*10 см. Метод предполагает испытания на излом. На заготовку воздействуют различными механизмами, а затем снимают полученные результаты. В рамках экспертизы анализируются изменения в состоянии материала под микроскопом, поведение сплава во время ударных нагрузок.В зависимости от цели исследования берутся разные виды профиля:
- V-образный используется для оценки эксплуатационных характеристик изделия. Такой профиль нашел применение в крупных сооружениях, имеющих важное значение.
- U-образный позволяет проверить на излом внутреннюю основу профиля.
- Т-образный нужен для проведения экспертизы образцов в условиях повышенного сопротивления к трещинам.
Проверка стали на излом
Это оценка ее способности сопротивления внезапным ударам и разрывам.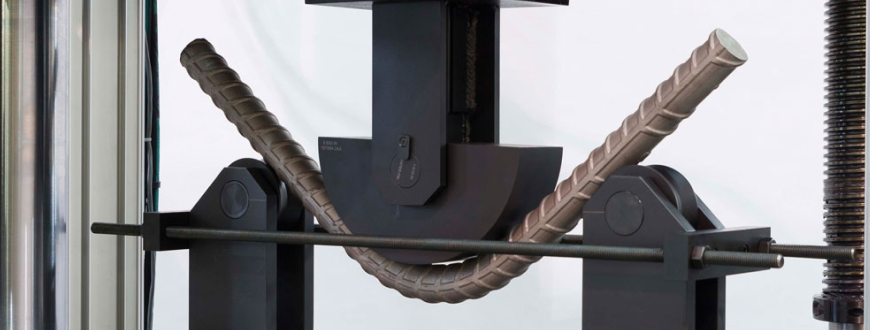
Основные методы исследования:
- Испытание Шарпи (Charpy Test). Тест позволяет измерить количество энергии, которое образец стали поглотит при ударе. В нормальных условиях (комнатная температура) ударная вязкость обычной углеродистой стали варьируется в пределах 50-200 Дж/см2. На холоде эти значения снижаются, а металл (труба, лист, проволока, арматура, сетка, пруток) становится более хрупким.
- Испытание Изода (Izod Test). Образец для испытаний (длина 75 мм, сечение 10*10 мм) с V-образным надрезом располагается под маятником. После удара молотка деталь ломается в районе насечки. Это позволяет рассчитать потенциальную энергию, которая передается от заряда к образцу.
Проверка на изгиб
Оценка способности стали выдерживать нагрузку на изгиб без образования дефектов на поверхности. Это особенно важно для конструкционных приложений, где деталь подвергается изгибающим нагрузкам.Разновидности испытаний:
- Трехточечный тест. Поддержка заготовки осуществляется на двух точках. Затем в ее центр прикладывается нагрузка. По нормативным параметрам для испытаний металл должен выдерживать изгиб до 180° (отсутствие трещин и деформаций на внешней стороне детали).
- Четырехточечный. Заготовка располагается на двух опорах, но на нее оказывают нагрузку в двух точках для более равномерного распределения напряжения по всей длине образца. Это наглядная демонстрация поведения оцинкованной, нержавеющей, алюминиевой и других видов стали при постоянном воздействии.
Механические методы испытания стали
Оценка образцов проводится с помощью следующих методик:
- Разрушающие. Получение данных происходит опытным путем в стенах лабораторий. При этом используют экстензометры, это специальные датчики деформации. Приборы служат для измерения степени повреждения, помогают рассчитывать рабочие показатели материала (сопротивление) в зависимости от нагрузки и силы воздействия. Датчик деформации бывает пневматический, лазерный, видео.
- Неразрушающие. Экспертиза оценивает магнитные и электрические характеристики материала. При этом целостность макроструктуры стали сохраняется в неизменном виде.
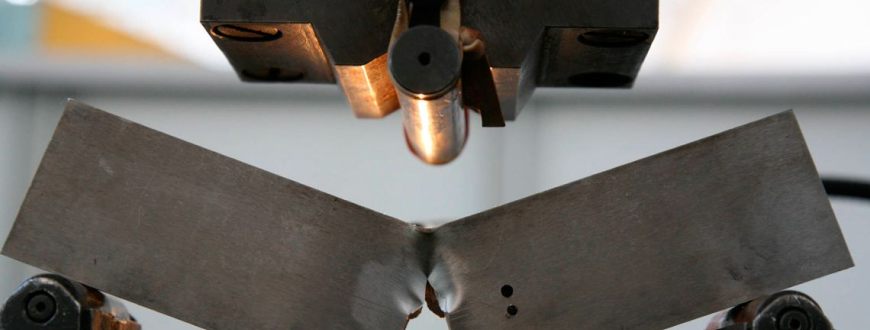
Проведенные исследования позволяют установить следующие параметры и пределы:
- пропорциональность – определение напряжения деформации в холоде, при котором закон Гука не выполняется
- прочность – выявление максимально возможной нагрузки до момента разрушения детали
- текучесть – характеризует напряжение, при котором рост пластических деформаций продолжается без увеличения нагрузки
- напряжение разрыва – реальные и условные значения, при которых заготовка начинает деформироваться
- пластичность – сравнение первичных параметров металла и значений, полученных после проведения анализа. Итоговый результат – разница между остаточным вытягиванием и сужением
Испытание на глубокую вытяжку
Исследование служит для определения степени растяжения листового металла. Применение метода показывает пригодность материала штамповке – при производстве подобные изделия подвергаются большой деформации.
Порядок исследования:
- Образец с круглым отверстием зажимается между двумя сферическими рабочими поверхностями. Лист фиксируется по радиусу прорези.
- Механизм воздействует на образец, вызывая продавливание отверстия.
- Оценка глубины проникновения шара, при которой не появляются трещины и другие признаки деформации.
Испытание на усталостную устойчивость
Параметр используется для определения способности металла выдерживать регулярные и систематические нагрузки. При этом усилие на образец прикладывается в разных направлениях (векторах).Исследование актуально для деталей, которые находятся под постоянно меняющимся напряжением (пружинные блоки, крепеж для строительных балок).
Для оценки устойчивости материала к подобным воздействиям следует подготовить рабочий стенд и создать нужные условия.Как проходит испытание:
- Образец зажимается в тисках.
- На свободный конец прикладываются разнонаправленные усилия. При этом важно не допустить разрушения детали.
- Выполнить множество циклов воздействия до нарушения целостности образца.
- Оценить усталостную прочность по времени до момента разрушения.
В зависимости от типа стали меняется и предел ее усталостной прочности. Аустенитные изделия показывают высокую устойчивость к многократным вибрационным нагрузкам. Марки стали с легированным ферритом, наоборот, покрываются трещинами от вибраций, но хорошо противостоят статическим воздействиям.
Испытание на сжатие
Показатель позволяет оценить, как ведет себя сталь под давлением. Метод необходим для определения момента начальной деформации или разрушения. Для проверки берется образец (куб). Его помещают под пресс для наблюдения. Вычисляется наибольшее давление, после которого деталь деформируется или разрушается.
Испытание на скручивание
Станок имеет две плоскости с тисками, расположенные параллельно друг другу. Образец (металлический пруток) фиксируется концами между ними. После включения оборудования идет скручивание детали на разной скорости и в разных направлениях до момента разрушения или разрыва арматуры.
Параметр показывает способность металлопроката или сплавов сопротивляться пластической деформации. При этом оцениваются характеристики именно внешних слоев материала.
Экспертиза стальных образцов на твердость упрощает оценку качества профиля после термической обработки.
Процедура проводится по разным методикам:
- Метод Бринелля. Стальной шар небольшого диаметра с разной силой вдавливается в плоскую рабочую поверхность. Это позволяет узнать точно параметр твердости (НВ), соотнести силу воздействия к размеру сферического отпечатка на поверхности.
- Метод Роквелла. В его основе лежат именно статические нагрузки, обозначается как HR. Стальной наконечник вдавливается в поверхность с разными усилиями, постепенно проникая через слои металла. Если материал имеет твердость до 450 HR, то роль стержня берет на себя шарик из стали, а полученную твердость обозначают как HRB. При значении более 450 HR применяется конус из алмаза (HRA или HRC).
- Метод Виккерса. Показатель твердости обозначается как HV. При анализе алмазная пирамида с четырьмя гранями вдавливается в стальную поверхность. Потом под микроскопом происходит измерение отпечатка (точность до тысячных долей миллиметра).
- Метод Шора. Твердость материала определяется после падения на нее бойка с заданной высоты. Расчет силы удара зависит от веса «снаряда» и высоты его отскакивания от поверхности.
Температурные испытания
При воздействии холода и нагревании металлические макроструктуры меняют свои свойства на короткое время. Вязкость, пластичность и твердость стали имеют отличия по положительных и отрицательных значениях. Поэтому нужна проверка характеристик прочности сплавов при разных температурных условиях. Это позволяет предугадать поведение готовых изделий во время эксплуатации.Схематично исследования проходят так:
- Образцы подвергаются разным режимам нагрева и охлаждения, при этом запускаются изменения макроструктур материала.
- Создается специальная карта с эксплуатационными значениями. В ней указываются температурные пределы, при которых свойства металла сохраняются. Отдельно выносятся критические значения, вызывающие разрушение или деформацию детали.
Химический анализ
В зависимости от типа стали меняется ее реакция на окружающую среду. На поверхности изделий при этом образуется оксидная пленка. Лишь ограниченное число металлов имеет высокую устойчивость к химическим реагентам (платина, золото, палладий). Остальные виды стали поражаются ржавчиной, которая проникает через микропоры, либо обзаводятся оксидной пленкой. Она сдерживает дальнейшее окисление.
Чистое железо при нормальных условиях вступает в реакцию практически со всеми кислотами и кислородом из воздуха.
Чтобы устранить этот недостаток при производстве стали в него добавляют другие металлы:
- хром
- никель
- марганец
Для проверки свойств готовых сплавов проводятся соответствующие испытания. При этом на образцы воздействуют различными химическими реагентами, меняя температурные режимы. Именно так создаются жаропрочные нержавеющие марки стали, а также сплавы, не восприимчивые к кислотам.
Металлографический анализ
Макроструктура стали на изломе имеет разные рисунки у каждого образца:
- крупнозернистая
- волокнистая
- шероховатая и т.д.
Неоднородность зависит от состава сплава. Строение стали, рассмотренное под микроскопом, помогает понять механизм появления коррозийной пленки. Во время исследования используют оборудование разной конструкции и степеней разрешения.
Дефектоскопия
Процесс металлообработки (литье, прокатка, сварка) не всегда проходит идеально. Продукция может иметь скрытые дефекты. Но в процессе обработки или во время эксплуатации подобные нарушения в микроструктуре материала нередко становятся причиной разрушения важных узлов и деталей.
Как выявляются дефекты:
- Рентгеноскопия. Просвечивание детали или образца рентгеновскими лучами. Короткие волны при излучении позволяют выявить микроскопические трещины, монолитные участки при этом выглядят как более темное пятно. Метод нашел применение при прокладке трубопроводов, возведении заводских труб, где важна высокая точность и надежность.
- Магнитоскопия. Метод актуален только для ферритных марок. Заготовка покрывается тонким слоем магнитного порошка. Места, где контакт между частицами менее плотный, выявляются по аномальным участкам на магнитном поле.
- Газоанализатор. Готовое изделие герметизируется, а затем наполняется специальным газом под давлением. После этого запускается сканирование поверхности газоанализатором. Проверка проводится с радоном для определения слабых мест.
- Ультразвуковое тестирование. На качественной заготовке наблюдается равномерное распространения коротких звуковых волн. Все дефекты создают препятствие, а детектор выявляет эти слабые места.
Спектральный анализ
Все элементы таблицы Менделеева имеют свою массу ядер и резонансную частоту колебаний. Во время спектрального анализа исследуется отклик сплава, облучаемого разной частотой. Это позволяет определить процентный состав всех химических элементов в образце.